OEM SERVICE
GLOBAL CUSTOMIZATION: TAPE OEM SOLUTION PROVIDER Aiya Tape as a leading tape manufacturer, focuses on providing high-quality OEM services for various industries. We have rich production experience and advanced technical equipment and can produce multiple types of tape products according to customer's specific needs and specifications, including double-sided tape, high-temperature tape,single-sided tape,Velcro,etc. | 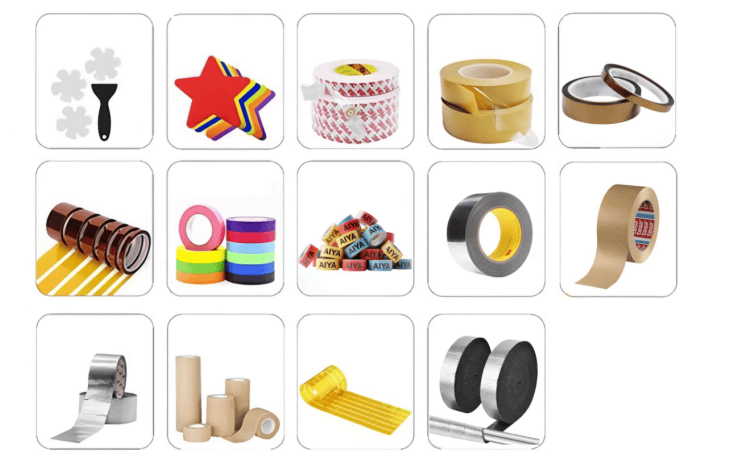
|
| MANUFACTURE In OEM cooperation, we partner with various brands, strictly controlling each step from design and material selection to production to meet brand requirements. Focused on quality and performance, we ensure stability via strict QC and advanced equipment. We see OEM as in-depth collaboration for mutual growth, committed to delivering excellent OEM services to promote industry progress. Aiya Tape centers on customers, offering professional technical support and after-sales service through our expert team. We've built long-term partnerships with renowned brands, aiding their rapid product iteration and market expansion via OEM collaboration. |
OEM CUSTOMIZATION FLOWCHART
1. Demand Collection: Contact clients to grasp business and product needs.
2. Design & Dev: Assemble a team to design and develop products, finalizing material, process, and structural plans.
3. Sample Making: Produce samples, test rigorously, submit to clients, incorporate feedback.
4. QC: Specialized team monitors production, rejects unqualified products.
5. Mass Prod: Start mass production post-sample approval, with strict quality control.
6. Delivery: Ship products per contract terms, ensuring safe transit.
| 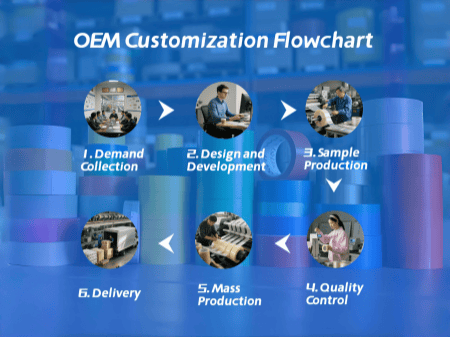
|
OVERVIEW OF AIYA TAPE OEM CAPABILITIES
1. R&D CAPABILITIES Aiya Tape's professional R&D team with deep industry expertise and advanced equipment quickly responds to customer needs. Focused on adhesive research and precision coating tech, the team drives innovation, optimizes products per market trends, and ensures new releases meet expectations via strict testing. | 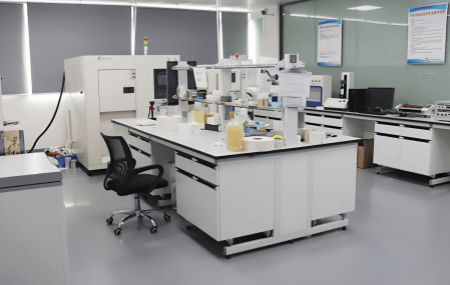
|
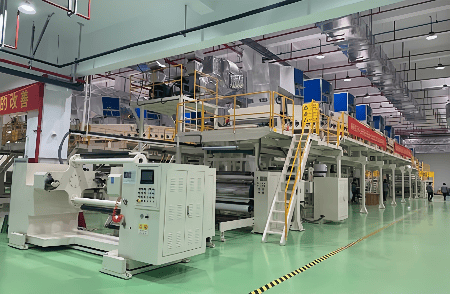
| 2. QUALITY CONTROL We've established a strict QC system covering all stages from raw material procurement to delivery, aiming for zero defects. Advanced equipment and process control ensure precise production, with multiple inspection points monitoring key nodes. Every product undergoes rigorous final checks on performance, appearance, and size. We promote employee involvement in quality management, driving continuous improvement to meet customer expectations. |
3. CUSTOMIZATION Aiya Tape emphasizes customer communication and cooperation, offering professional customized services to meet unique needs. With flexible production lines, we tailor product specifications—from standard to special sizes—rapidly. Our R&D team adjusts performance parameters per industry applications, while personalized packaging solutions ensure optimal product preservation. A dedicated customer service team maintains close communication to deliver full-range customized solutions, earning customer trust through tailored support. | 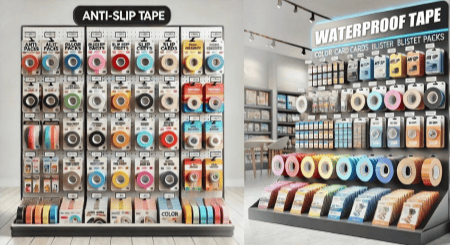
|
OEM CASES CUSTOMIZED BY CUSTOMERS
CASE 1: CUSTOMIZATION OF HIGH-PRECISION ELECTRONIC TAPE Description: A renowned electronics manufacturer needed high-precision tape with specific viscosity, heat resistance, and insulation. Aiya Tape, leveraging advanced equipment, customized the tape by strictly controlling raw materials and production. The solution met performance needs, enhanced production efficiency, and won high praise. | 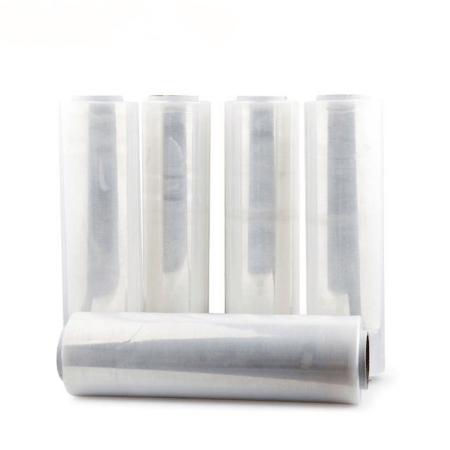
|
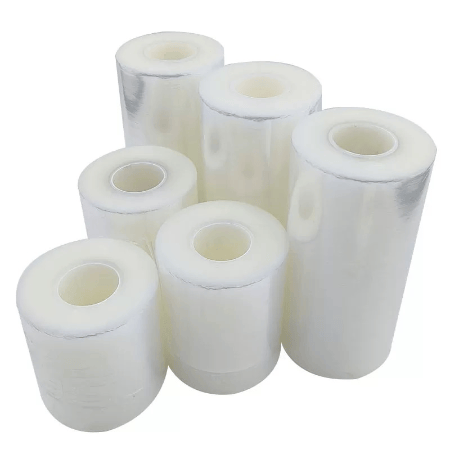
| CASE 2: DEVELOPMENT OF ENVIRONMENTALLY FRIENDLY PACKAGING FILM Description: An environmentally friendly food company seeks a degradable and non-toxic packaging film. Aiya Tape responded quickly and used its own R&D strength to develop an environmentally friendly packaging film that meets customer needs. We focus on the environmental performance of the product while ensuring the durability and aesthetics of the film. This film has been widely praised in the market and helped customers enhance their brand image. |
CASE 3: PRODUCTION OF SPECIAL ADHESIVE TAPE FOR AUTOMOBILES Description: An automaker required high-strength, wear- and heat-resistant adhesive tape. Aiya Tape adjusted processes and formulas per needs, producing compliant tape. Close communication ensured performance optimization for stability in auto manufacturing. The tape became a key production-line component, enhancing efficiency and quality. | 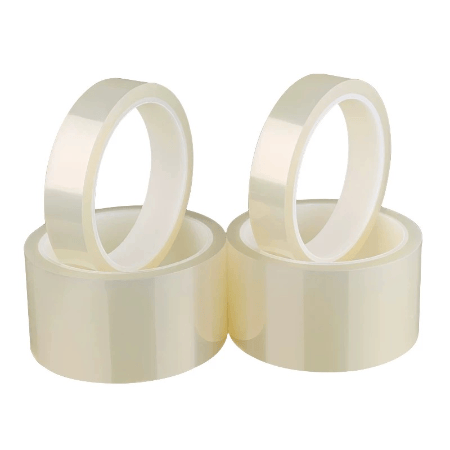
|
RESEARCH AND DEVELOPMENT
Xiamen Aiya Tape Co., Ltd. is a diversified group company, including industrial tape business, film products business, die cutting division. Aiya Tape is an innovative production enterprise integrating research and development, production and sales, with a research and development team of adhesives and precision coating technology, with the application of the whole process solution.
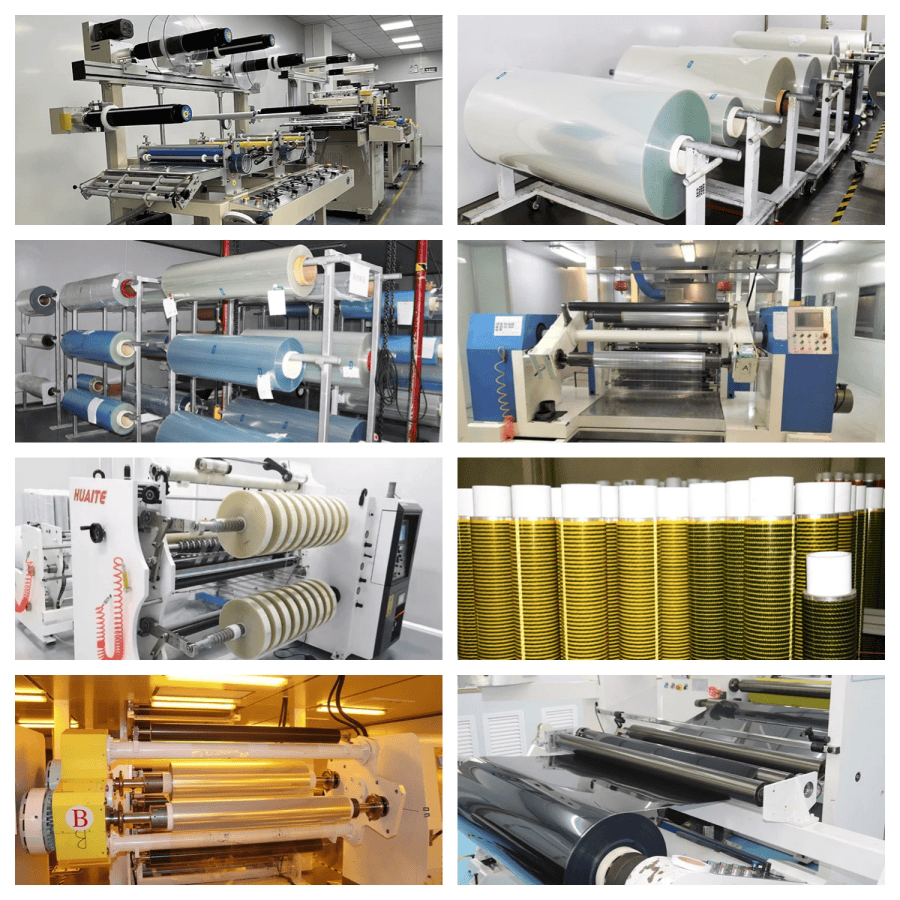